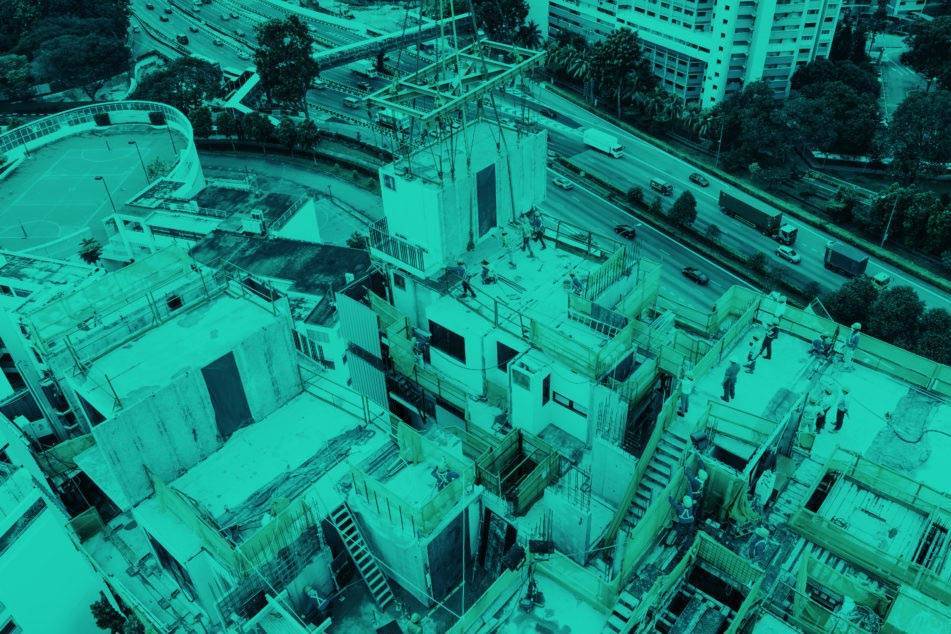
Modular construction
Singapore. Modular construction on the rise.
SINGAPORE. In the Clement Canopy project, Bouygues Construction, via it’s subisdiary Dragages Singapore (Bouygues Bâtiment International) is building the tallest towers ever erected using modular concrete and positioning itself as a leader in this very promising market.
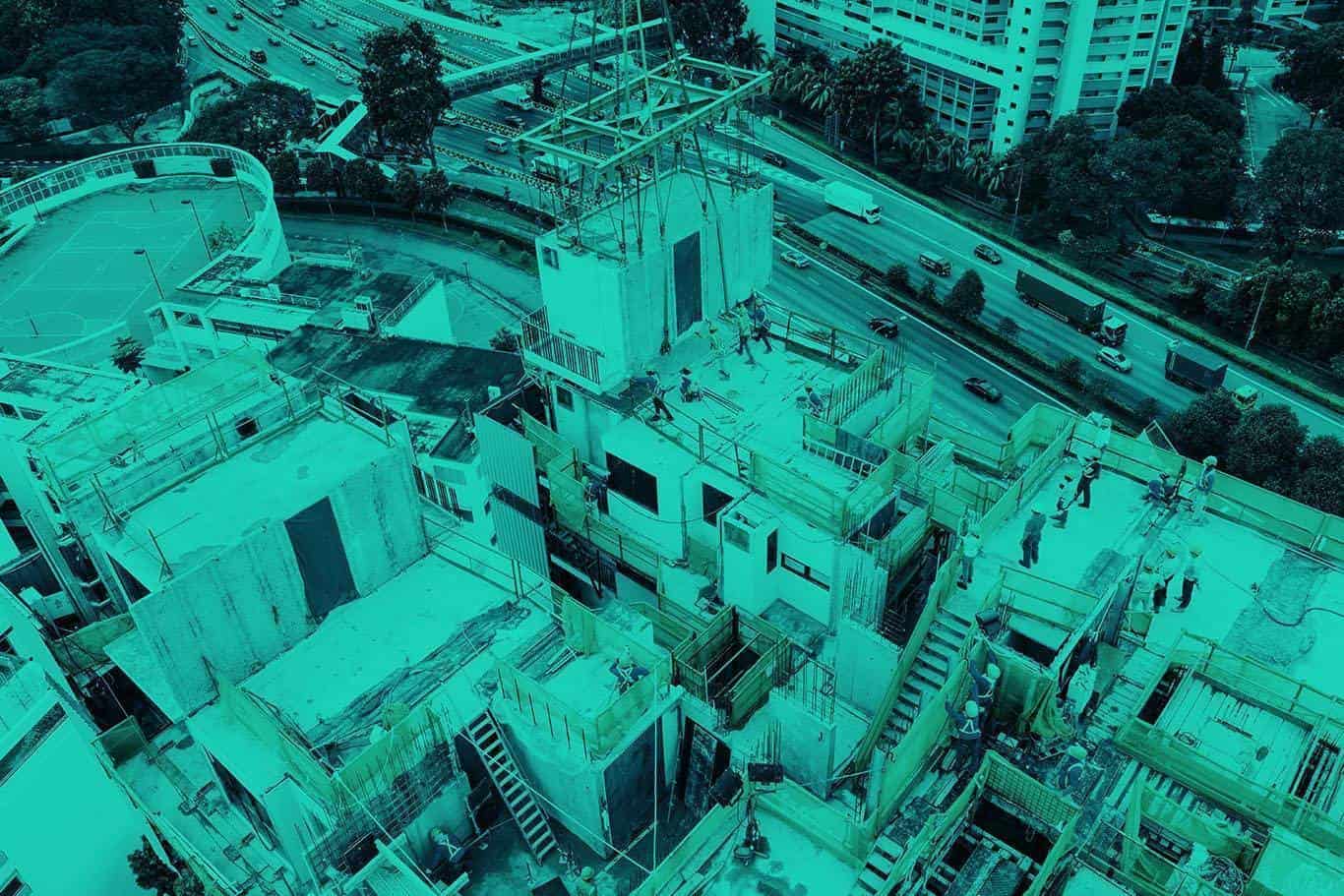
Édito
On-site construction is going to change a great deal in the next few years by increasingly integrating off-site construction, whether it is for the prefabrication of architectural elements like balconies and façades or technical elements – the conduits, bathrooms, and so on – or at the highest level, which is PPVC. Modular construction is already revolutionizing the construction sector. In the future, it will provide a response to fundamental trends, which are mass production, prefabrication, digitization, and the circular economy.
Products that lend themselves easily to this type of construction are hotels, student residences, nursing homes and hospital
rooms. These are particularly well adapted to modular construction because the room and the module are the same size, which is optimal for transport and installation.
In parallel, we are continuing our research and development on our construction methods, using innovative materials to reduce the weight and cost of the modules.
As a global player in property development and construction, Bouygues Bâtiment International is the only company that offers its customers an all-inclusive approach, from the technical feasibility studies to the handover of the project. This includes handling all aspects of production: module fabrication, transport, logistics, installation, and coordination of all trades on site.
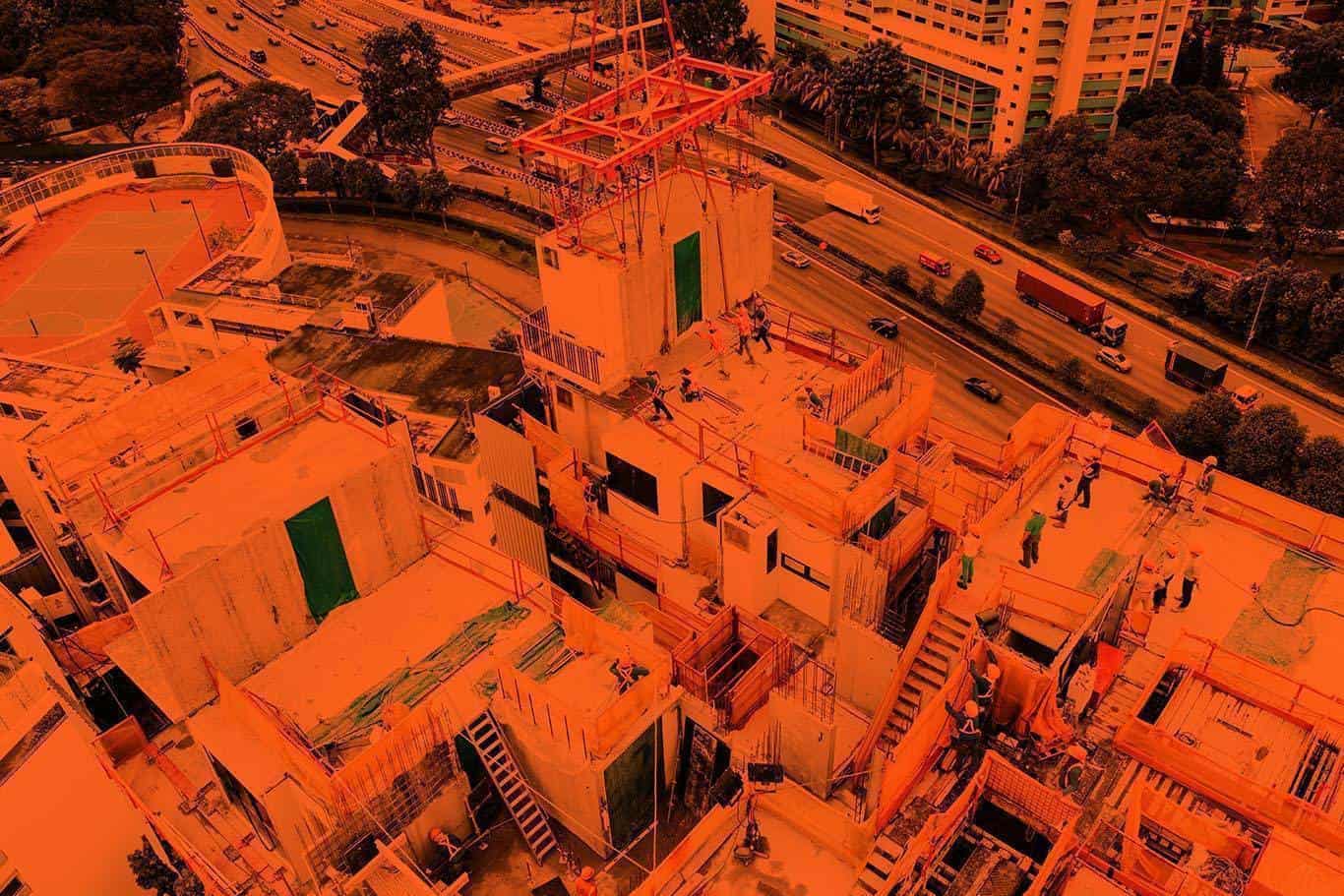
Challenge accepted
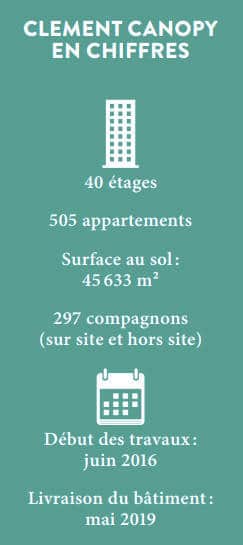
Alagusundaram Palaniappan is supervising the installation of a concrete module in the Clement Canopy project, in which two 140 meter residential towers are being constructed in the Jurong Lake student quarter in a western neighborhood of
the capital. The chief surveyor is watching to see that the tricky operation goes off smoothly. A precast module weighing
23 tons is being lifted to the seventeenth floor of one tower so that it can be placed on the top of the other. Several things immediately strike one as unusual. First, only two men are involved in lifting the module; then a small team of just four men set it in place in ten minutes. There is no noise of trucks transporting materials, no dust produced by concreting operations, and no scraps of steel or plastic packaging visible anywhere.
Chief surveyor Alagusundaram Palaniappan (left) and Paul Joginder, Deputy superintendent director, at the Clement Canopy worksite.
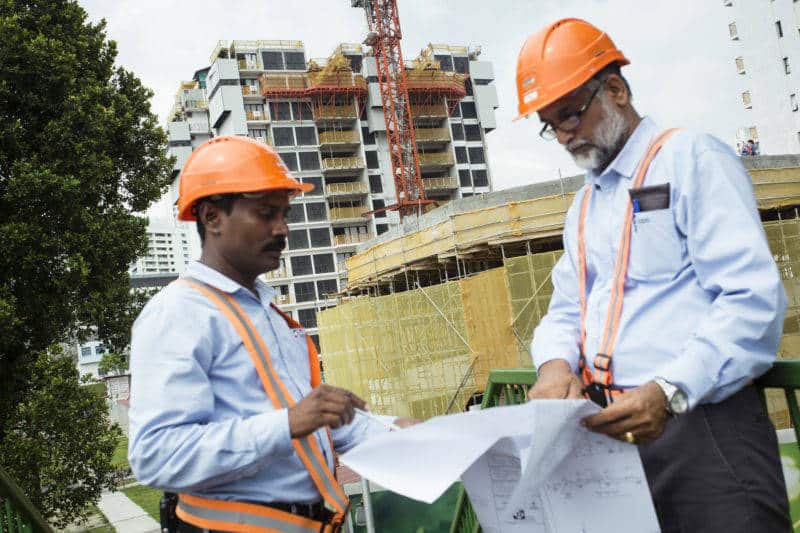
Clearly, Clement Canopy is different from other projects. It is being carried out with a modular construction technique, or more precisely, with Prefabricated Prefinished Volumetric Construction (PPVC), as it is called in Singapore. The blocks that make up the building are prefabricated and mostly finished both inside and out at plants offsite. They are then brought here and assembled. This technique is very popular with the Singapore government, which is eager to increase productivity in the construction sector and is now demanding in many projects that 65 percent of the building superstructures be constructed with PPVC.
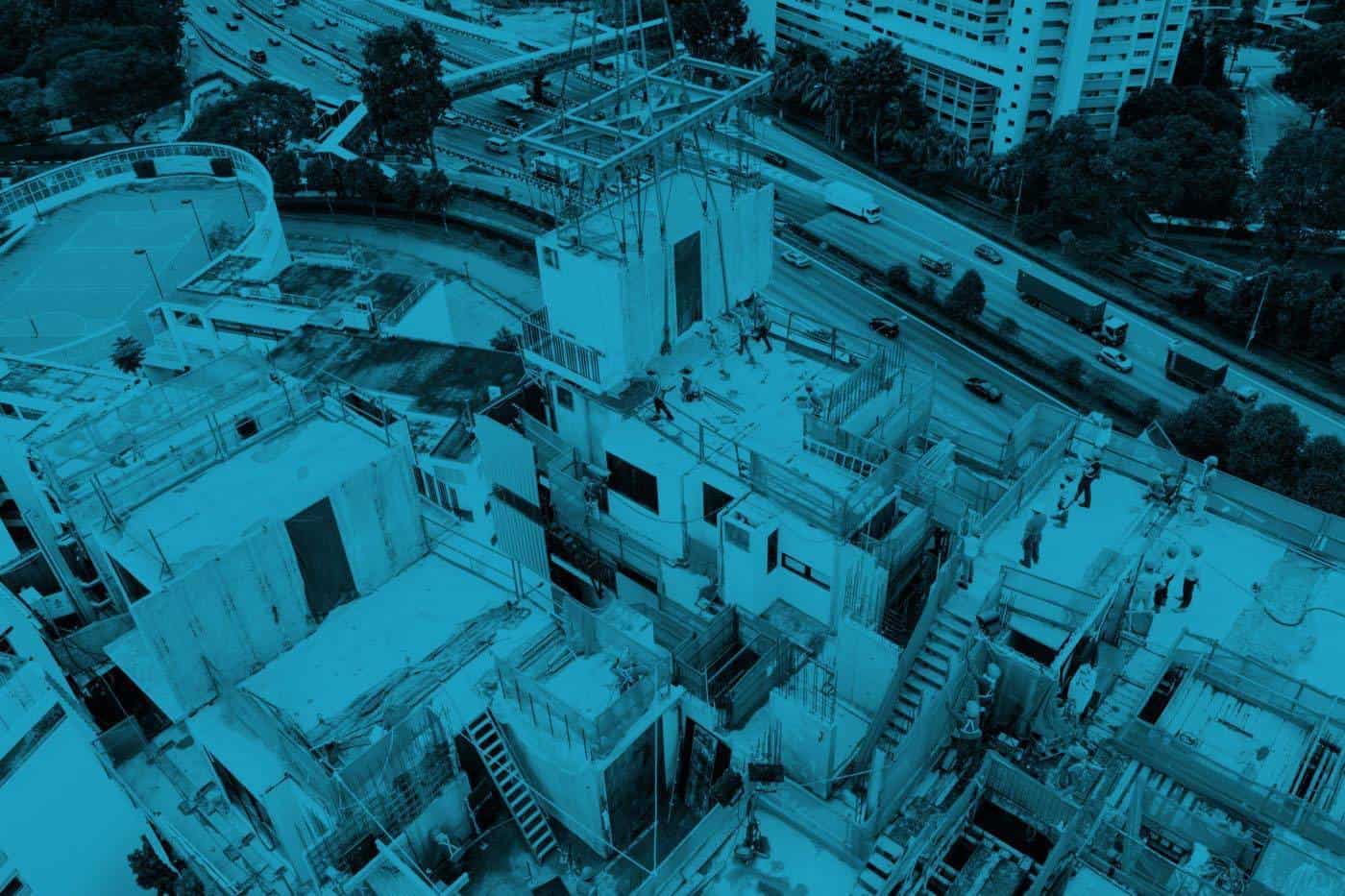
Never seen before
“We certainly welcome Dragages Singapore’s very proactive stance in leading the productivity movement in our construction sector.”
‐ Lawrence Wong, Minister for National Development and Second Minister for Finance Singapore Government
Dragages Singapore’s know-how in PPVC comes from experience acquired in the 2014 extension of the Crowne Plaza Hotel, the first project of its kind in Singapore, and in the construction a year later of an assisted living facility, the Woodlands
Crescent Nursing Home. Nevertheless, the Clement Canopy project presents some new challenges. The loadbearing
steel structure that supports the modules in the previous projects is replaced here by reinforced concrete, a material preferred by the buildings’future owners because of its durability. The materials are also heavier, meaning that two cranes capable of lifting modules weighing up to 31 tons had to be brought from Germany.
A prefabricated module is lifted on the Clement Canopy worksite at Singapore.
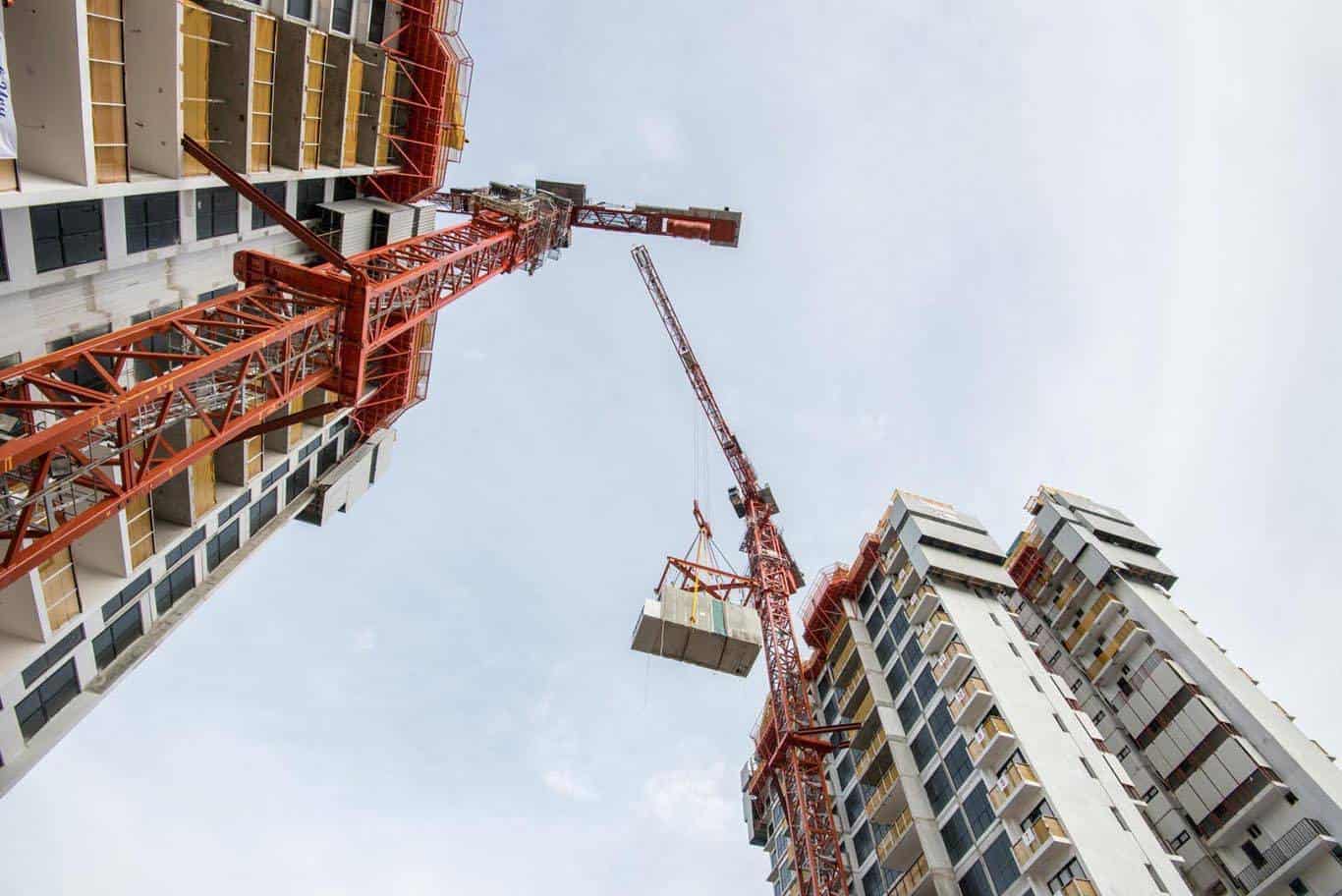
“It’s quite simple. Constructing a tower this high, with this quantity of concrete modules – 1,866 in all – with walls barely 8 centimeters thick, is an all-time first anywhere in the world,” explains Allan Tan, executive director of Dragages Singapore.
“Stacking modules one on top of another like Lego blocks might seem like child’s play, but that’s not the case at all,” adds Seng Swear Wern, the production manager on the project. “This operation calls for the precision of a goldsmith, with a tolerance of two millimeters for the joints between the modules. Anything greater would threaten the building’s stability.”
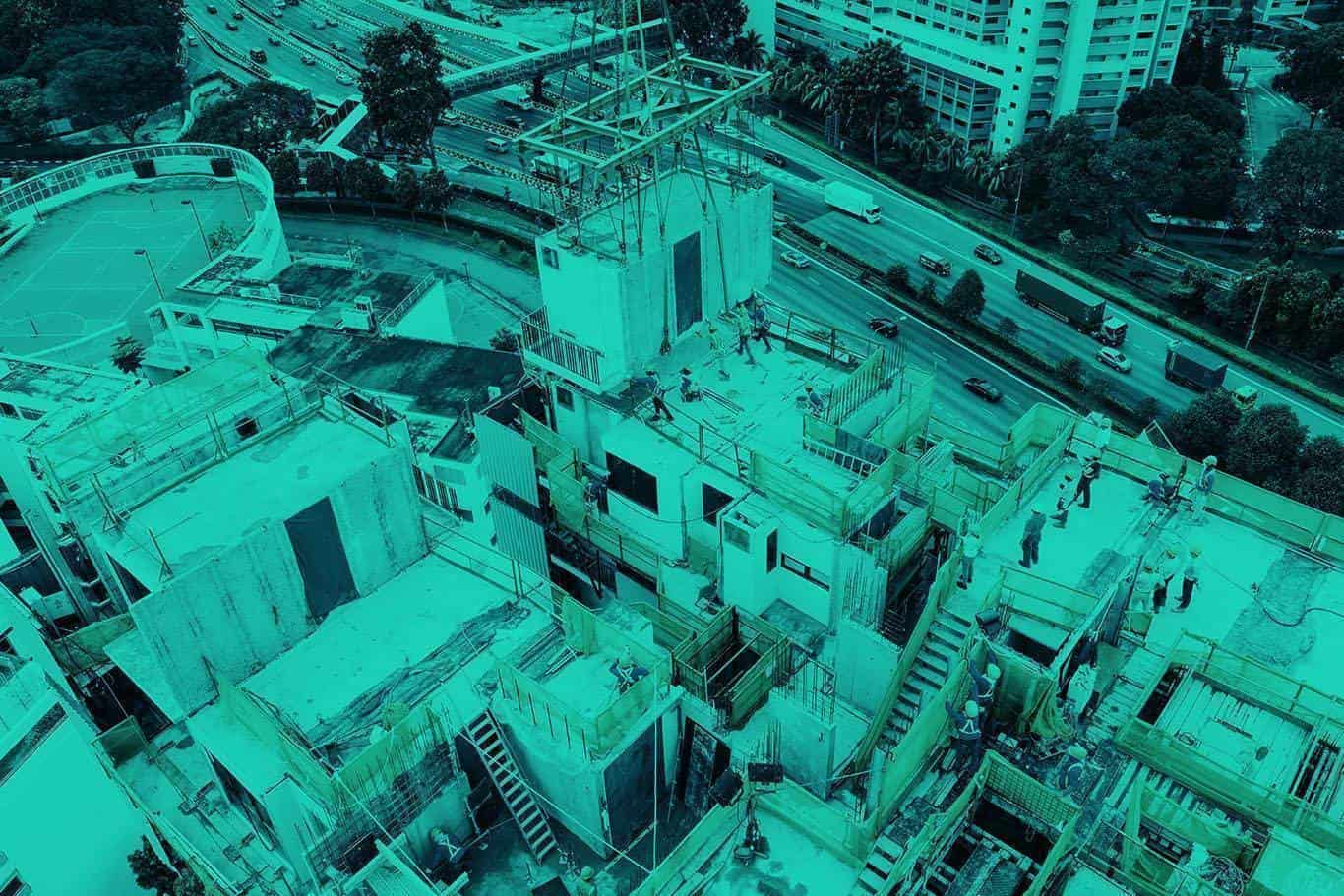
Outfitted head to toe
Checking that the modules are aligned and that the mortar poured between them is up to standard; seeing that deadlines and safety instructions are respected: nothing escapes the eye of Palani and his coworkers at the top of the tower, where four modules are installed each day. They are performers in a continuous ballet orchestrated according to a meticulous strategy in terms of planning and logistics. And that is also true at the first link in the module production chain, sixty kilometers from here in Senai, Malaysia, where they are cast, and at the Tuas plant, west of Singapore, where the finishing work is done.
The plant at Senai, Malaysia, where modules are precast for the Clement Canopy project.
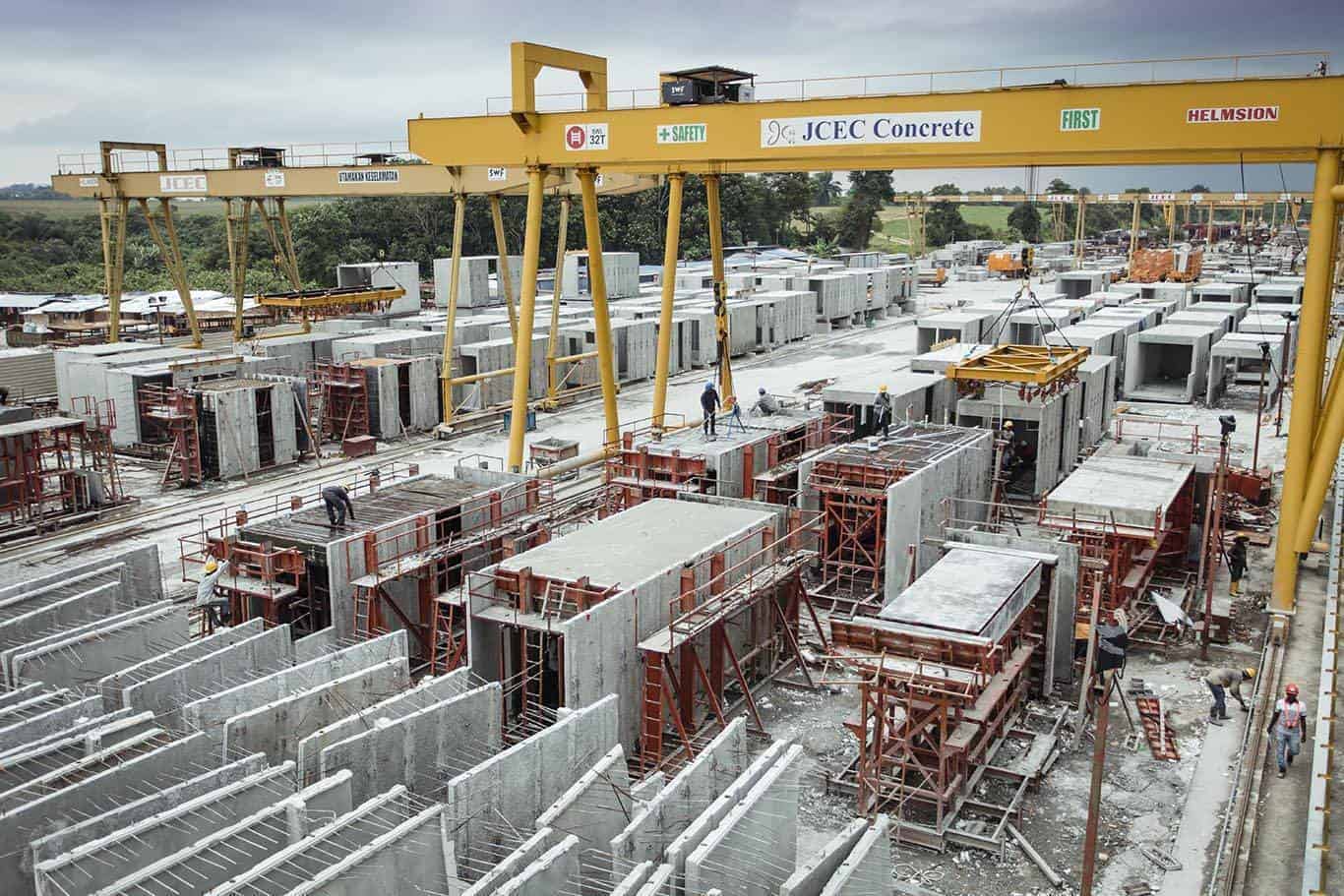
In fact, the first module installed this morning, measuring 22 sq. meters and containing a main bedroom, a bathroom, and
a toilet, arrived from Tuas yesterday, with its windows, doors, floor and wall coverings, closets, shower, mirror, electrical outlets, switches, and air conditioning already installed, with all the plastering and painting done, and with everything from floor to ceiling tested. All these operations are performed offsite and under roof, which allows the Dragages Singapore workers to better control the work environment.
The plant at Tuas, in western Singapore, where the finishing work is done on the modules for the Clement Canopy project.
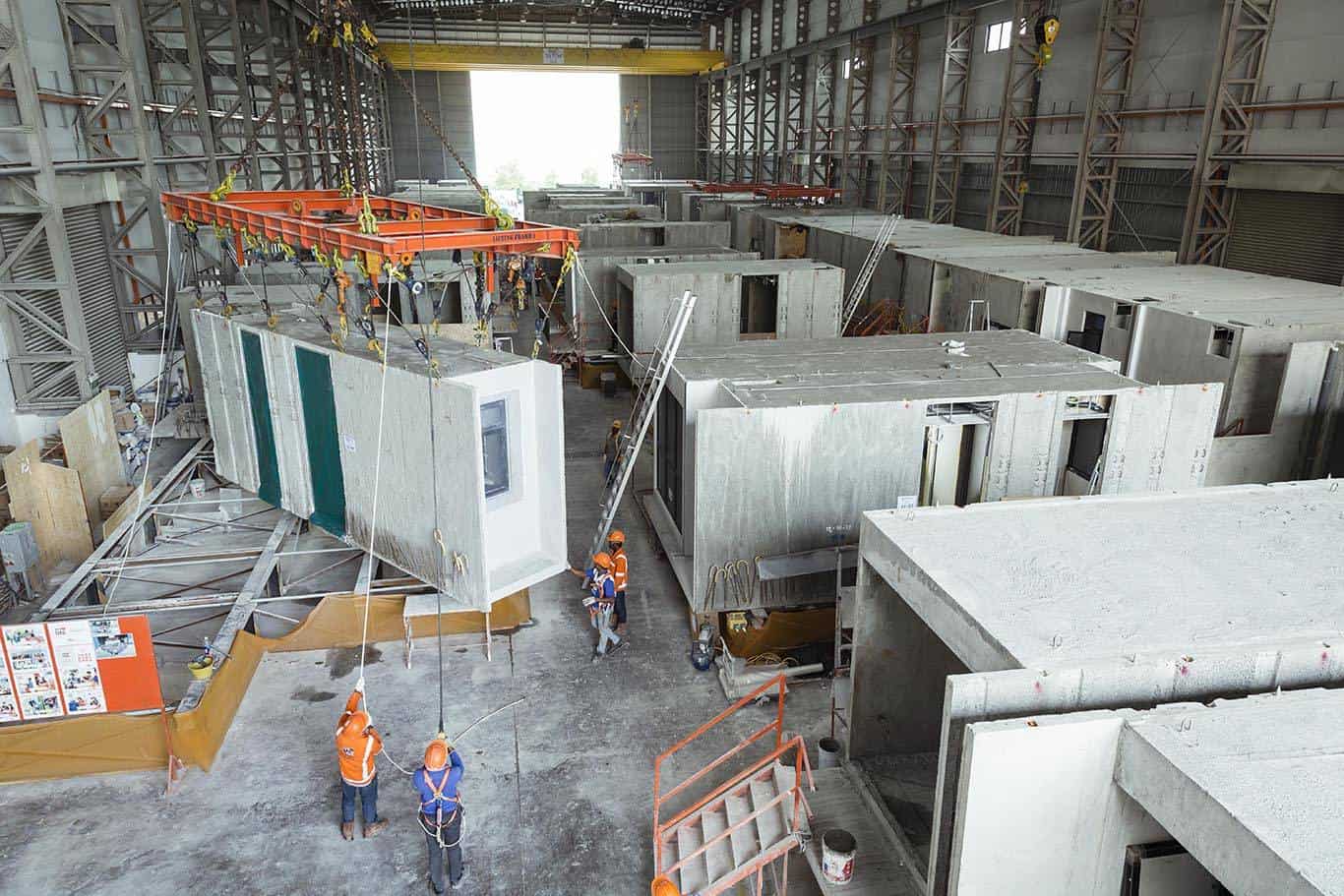
By Ludmilla Intravaia, in the Minorange. Photographies : Arnaud Février, Minorange.
PPVC has many advantages: construction time reduced by up to 50 percent, 30 percent fewer workers on site, less noise pollution, improved worksite safety and a higher-quality finished product, plus the possibility of reusing materials in a circular economy approach. Julien Esch, director of Dragages Singapore, Vietnam, Indonesia and Malaysia at Bouygues
Bâtiment International (a subsidiary of Bouygues Construction), says, “This innovative construction method is a key
added value for Dragages Singapore, which is now positioned as a leader in this very promising market.”