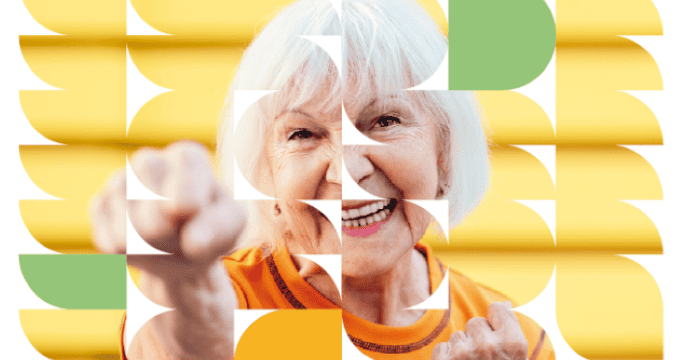
Building schools in modular wood
6 minutes of reading
Interview with Marina Da Silva Carvalhais, R&D projects and Wood Construction Innovations (WeWood).
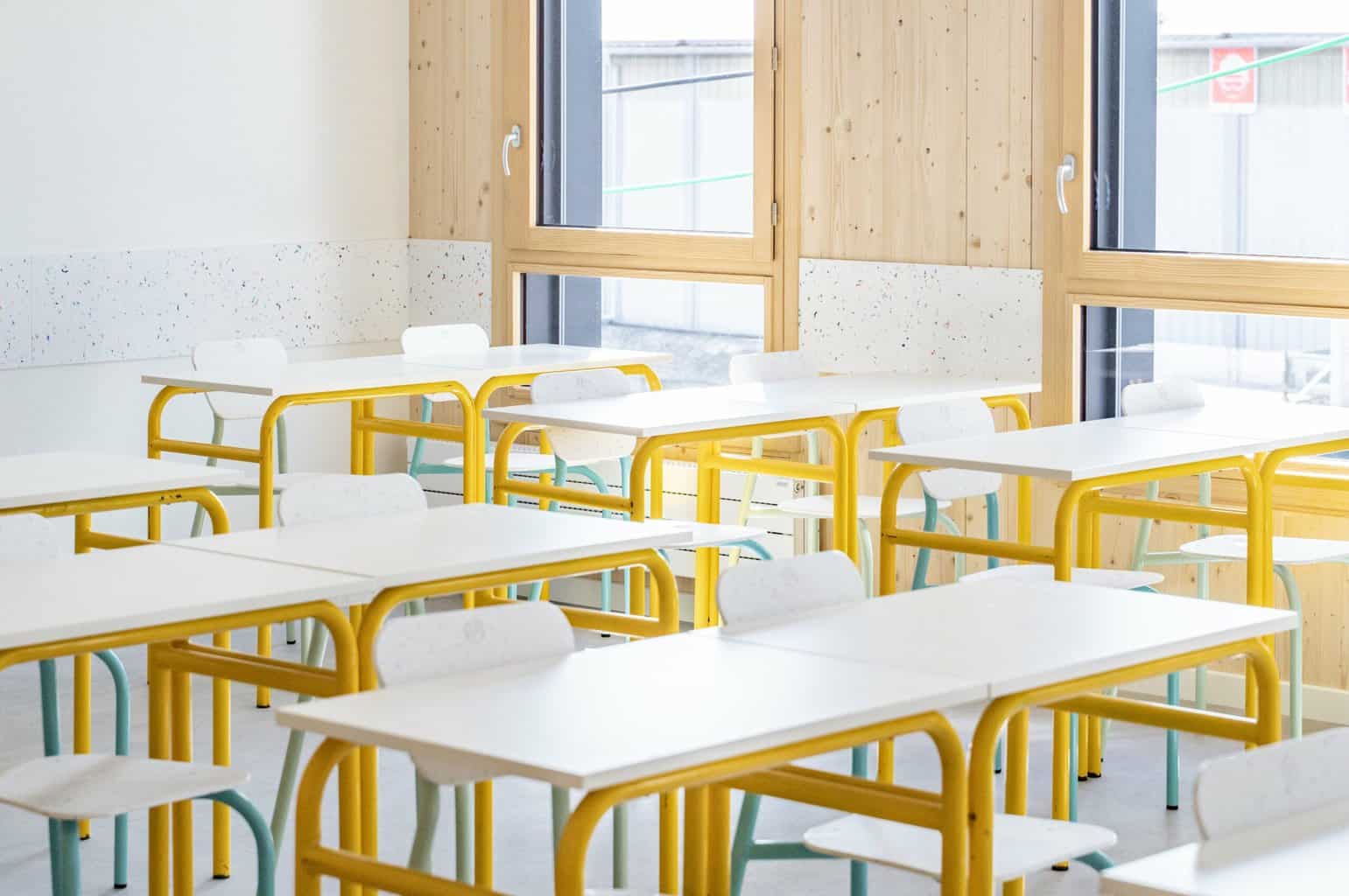
Why should we rethink the design and construction of schools, colleges and high schools?
Today, in France, a significant majority of these buildings are built on site, and still primarily as concrete structures. But the environmental situation we are experiencing is compelling us to change, and in particular to increase our use of wood construction and off-site construction. Bouygues Bâtiment France also aims to achieve a 30% share for its wood projects by 2030, and McKinsey expects a 20% share of global construction to be moved to off-site construction by this same deadline. On the other hand, the “traditional” method of constructing this infrastructure often generates nuisances for the inhabitants and the communities: noise, dust, odours, increased road traffic, etc. Contracting authorities and companies naturally seek to limit these nuisances. Off-site construction makes this possible, while shortening the duration of on-site work, and improving conditions for craftsmen: sheltered from bad weather in a workshop, working with wood rather than concrete, etc. But when building school equipment partly off-site using wooden structures, it is essential to plan this construction method from the start of the design. This is possible when working on design-build projects, and assuming all project stakeholders share the same ambition,and project management in particular. Local authorities also expect ever less carbon-intensive and more scalable school development projects that are capable of adapting to demographic changes in their regions.What does the solution developed by BBF consist of?
In a project partnership between Bouygues Bâtiment Industrie et Equipements Publics, WeWood and the manufacturer Technologies & Habitats (T&H), we designed a solution of wooden classroom modules that are prefabricated and pre-equipped in the factory. The particularity of this solution is that it is not only the structure, the envelope of the classroom that is prefabricated: we have conceived it as a space – a product that is all but completed in the factory – incorporating as many ancillary services as possible, to be “plugged into” the general infrastructure. And why focus on classrooms? Because with standard needs and recurring programmes from one project to another, classrooms – which represent about 50% of the surface of a secondary school building – are ideally suited to the design of a modular construction product, as well as industrial production. We have therefore closely examined the programmes of many high schools and colleges to identify the specifications of a typical classroom. Considering criteria for technical facilities, interior finishes, acoustics, fire safety and ceiling height, and adopting the most demanding constraints where applicable. This led us to work in five areas:- Floorspace management and architectural principles of façades;
- Sizing of structural elements;
- Integration of technical terminals and networks, feasibility and interfaces with the technical trades for the rest of the building conducted on site;
- Incorporation of architectural building trades, feasibility and limits of services;
- Implementation methods (supply, quality control, temporary watertightness, lifting, etc.)
What are the advantages of this solution in terms of reducing the carbon impact?
These classrooms benefit from the know-how of WeWood, the wood expertise centre of Bouygues Bâtiment France. Each module uses 140 kg of biosourced materials per m², or 4 times the value of the highest performance level of the “Biosourcé Building” label. With this material, the carbon impact of the construction is reduced by 170 kg CO2e/m² compared to a concrete construction, or nearly 25% in Life Cycle Analysis. The European wood used, labelled PEFC or FSC, comes from a sustainable sector managed to combine reduction of the building’s carbon footprint, comfort of use and well-being thanks to the apparent material. Once delivered, the modular construction is compatible with the 2031 threshold of the RE 2020. This threshold, the most ambitious of the regulations, limits the carbon impact of school energy consumption to 140 kg CO2/m² during their operation.Where are we on the development and deployment?
After 18 months of R&D with TH we have built a prototype which is currently installed on our BYCN Hardware base in Chilly-Mazarin. It is a demonstrator on 2 levels of a classroom of 55 m² and a work room of 39 m². This allows us to verify certain performances, notably acoustics and air tightness, but also and especially to show concretely what this solution can make and prove that industrialization can rhyme with high quality.What do you think the construction of public facilities will look like in 2030?
France will have to meet its national targets for reducing greenhouse gas emissions, and labels will become ever-more demanding: construction methods will therefore need to evolve so that our buildings set a better and better example from an environmental point of view. I see it as involving more wood, of course, with the use of concrete limited to strictly necessary places such as foundations, infrastructure and areas where the architectural concept and the technical and scheduling requirements justify its use. I also imagine we will see less reticence over the use of other bio and geosourced materials such as hemp, or raw earth. And, of course, as envisioned by the McKinsey report in 2030, I see it as being partially carried out off-site. Because I don’t believe in buildings that are entirely prefabricated in the factory, at least not for the moment: off-site construction will be used where it is most relevant, and in particular in classrooms! Projects will be faster, and will generate less nuisance for residents, for the environment, and for site workers. Public facilities, such as a school, college or high school, are designed to play a specific role in local urban life; and I believe it is essential for them to be in harmony with that life, starting from the construction phase.More reading
Read also
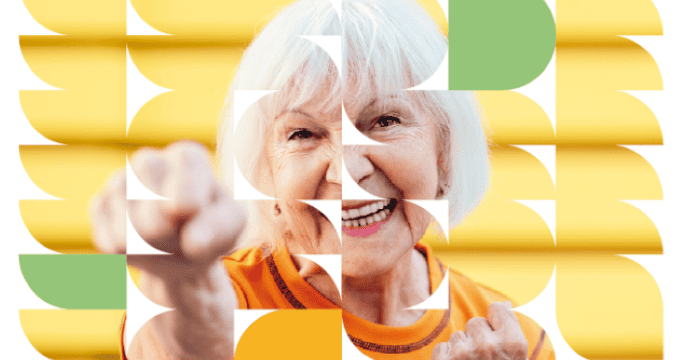
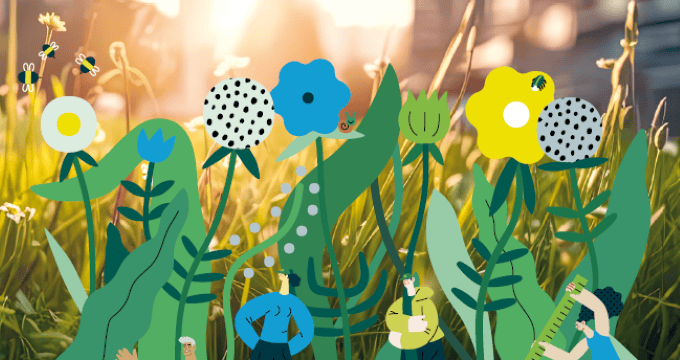
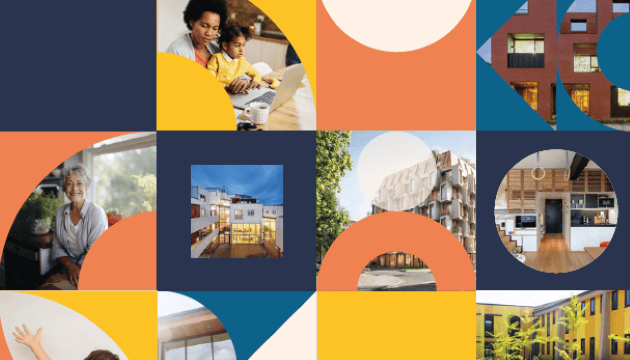
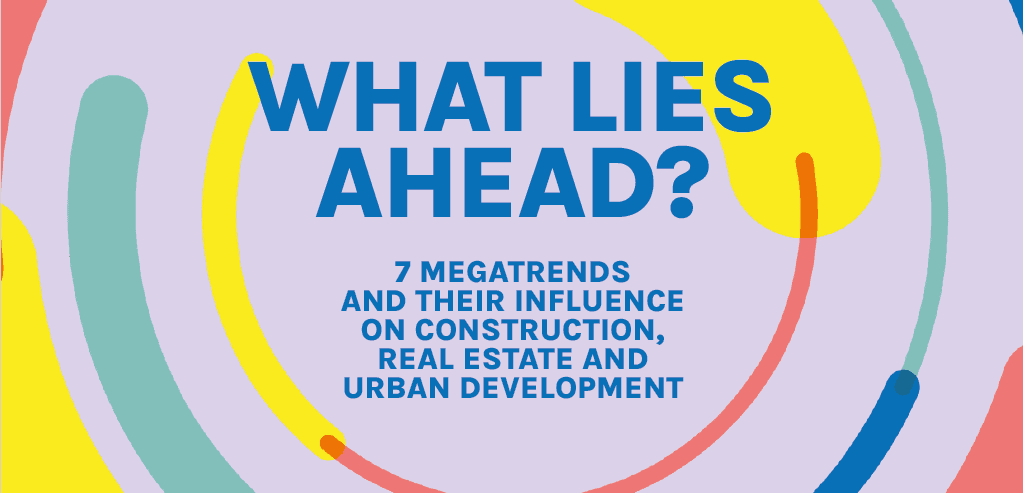
What lies ahead? 7 megatrends and their influence on construction, real estate and urban development
Article
20 minutes of reading