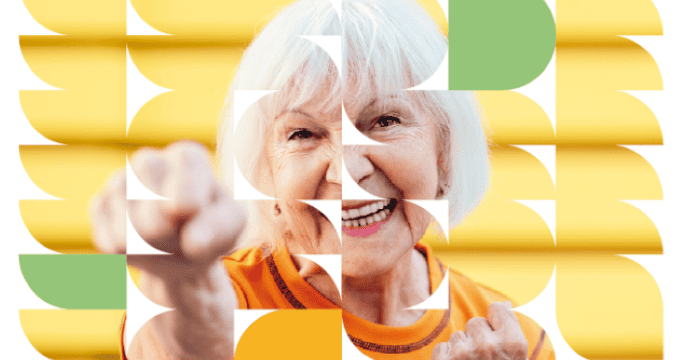
Laure Abdul, PhD in Materials Engineering, presents the concept of soil cement.
4 minutes of reading
Given the backdrop of depleting resources such as sand and the saturation of landfills in Île-de-France, and due to the volumes excavated for this work, the idea of reusing the land excavated for new construction was very appealing.
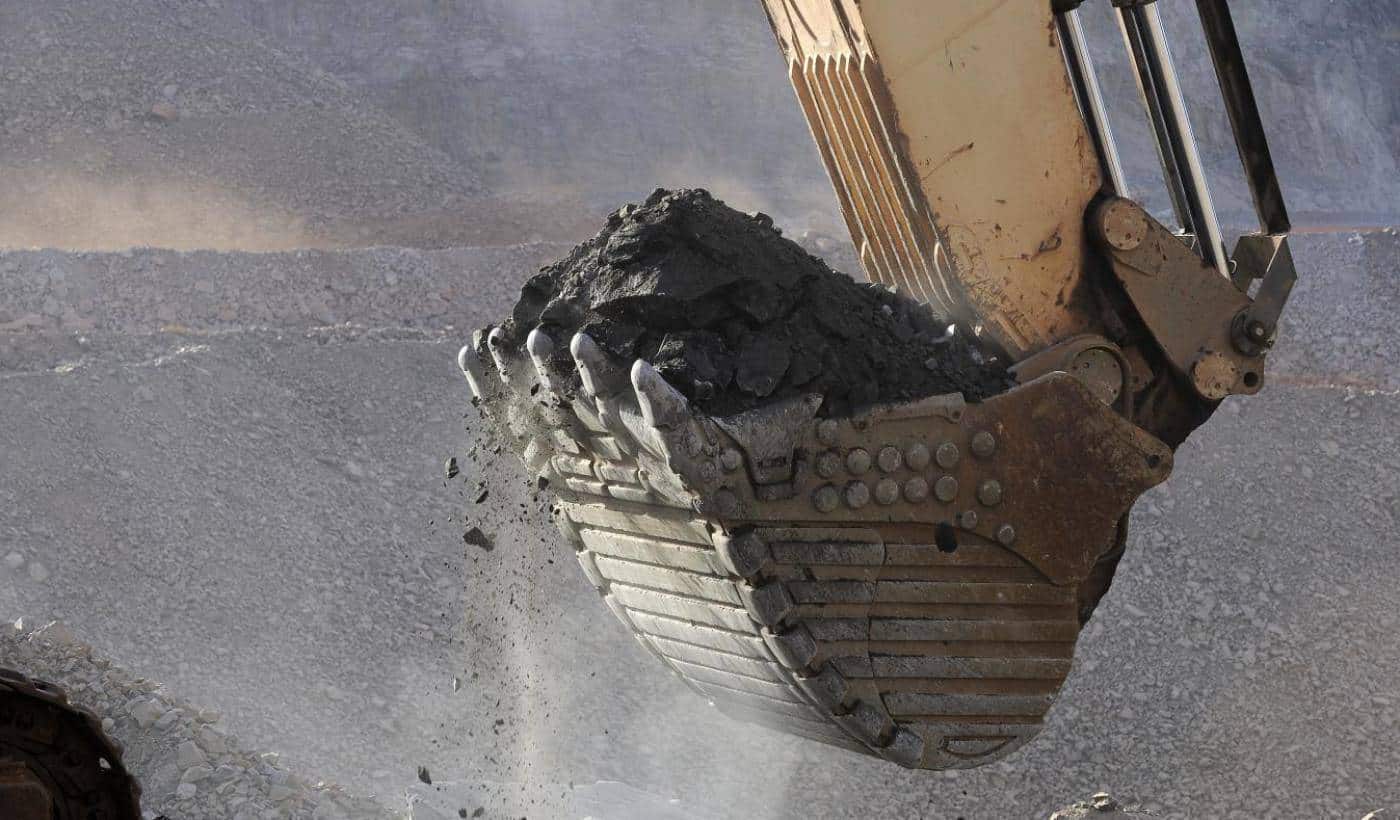
Led by Laure Abdul, who holds a PhD in Materials Engineering, the research project concerning the concept of soil cement is being carried out within the Materials Engineering Division, a Bouygues Construction/Bouygues Travaux Publics centre of excellence. This project aims to reuse excavated soil as sand for concrete. Can you explain to us how this project was conceived ?
In the context of Bouygues Construction’s partnership with BASF, a German chemical company, we began by studying the changes in the soil extracted during tunnelling. This soil receives a special chemical conditioning agent, such as injected foam for example, which is necessary for the progress of the tunnel boring machine. In order to properly select these products, we needed to understand the changes they brought about in the properties of the excavated soil, both in the short and long term. After a period of several days, no significant impact was found on the soil.
In early 2016, with the Grand Paris (Greater Paris) project approaching, we then reflected on how we could reuse this excavated soil, commonly known as spoil. Given the backdrop of depleting resources such as sand and the saturation of landfills in Île-de-France, and due to the volumes excavated for this work, the idea of reusing the land excavated for new construction was very appealing.
For about two years now, the PIM has been conducting research to remove any barriers and allow the reuse of excavated spoil in concrete. What exactly is it?
It is critical to understand that there are several types of excavated soil, and in particular several types of sand. For standard sand, whether it has received a conditioning agent or not, reuse does not pose any particular problem because the performance is not impacted. On the other hand, in Ile-de-France, Beauchamp sand is widely present, particularly where the work concerning line 14 is located and in the north; this sand has the distinctive feature of being loaded with clay, which makes it very absorbent and can have a real impact on its properties. The conditioning agent is not the problem, it’s the clay content.
In 2017, we realised that Colas was using a concrete admixture for clay, called MasterSuna, manufactured by our partner BASF to treat the crushed sand from some of their quarries. We then began to research if we could use it on the Beauchamp sand to allow us to manufacture concrete with favourable properties.
Two experimental campaigns are being conducted this year with the aim of defining the optimum amount of the additive to use depending on the amount of clay present. The consistency of the fresh concrete is tested to verify that it allows implementation on site for 1 hour and 30 minutes after production. The condition of the hardened concrete is also tested to measure mechanical properties, as well as dimensional variations, durability and hardness. Accelerated testing exists and lasts about three months.
The first campaign was not completely satisfactory. The mechanical properties of the hardened state complied with the reference concrete, but maintaining the consistency of the fresh state was problematic. Following research carried out in close collaboration with BASF, a new version of the admixture will be released in 2019. Given the mechanical properties obtained, this concrete could have any type of use.
In addition to this research on the material itself, have you encountered other problems related to the deployment of soil cement?
In addition to the properties of the material itself, site logistics is also important because there is a real problem concerning storage. In the Paris region, construction sites have little room for storage nearby. This sand could be used on the construction sites of nearby stations, or it could be used for items that are prefabricated in a factory and which will then be brought to other building sites. It’s all about saving resources.
Investigating the different ways to optimise the use of soil cement is one of the next steps in the project. Our participation in the innovation competition was also intended to publicise the project within the Group, with the aim of perhaps welcoming new partners and new skills focused on logistics, for example.
More reading
Read also
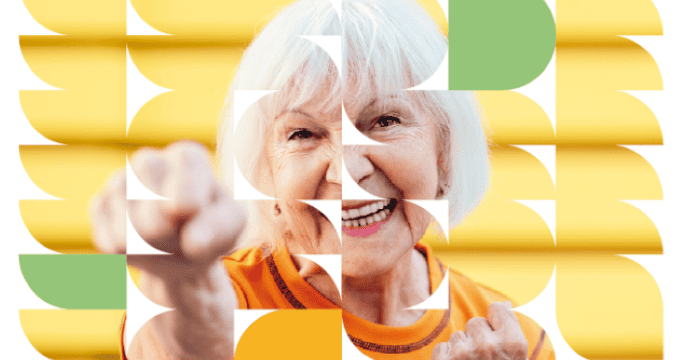
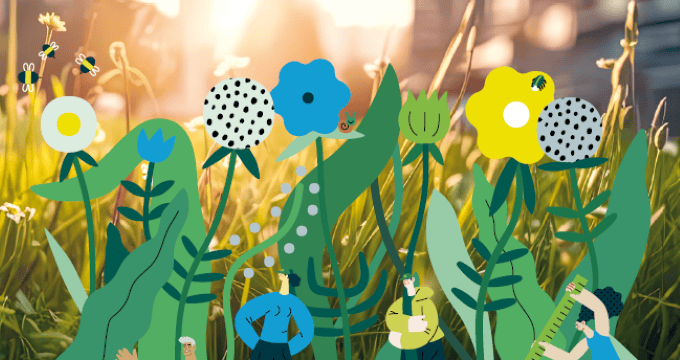
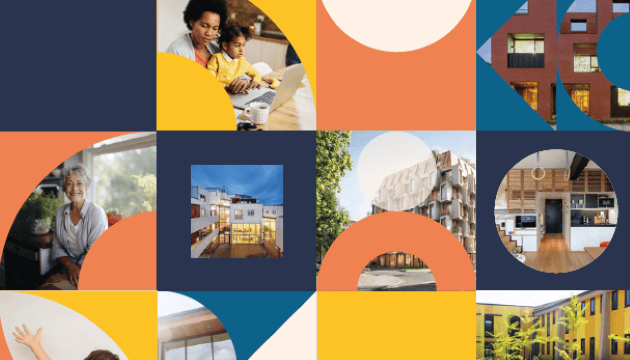
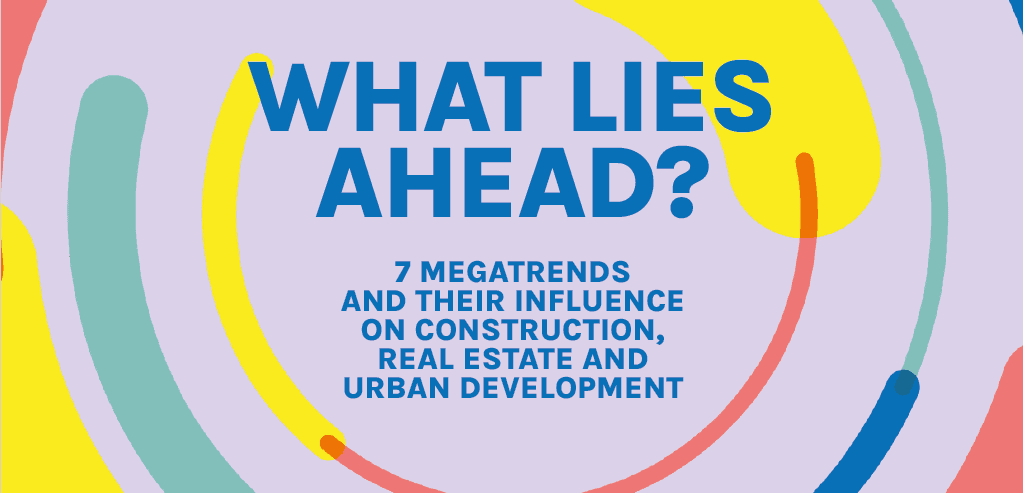
What lies ahead? 7 megatrends and their influence on construction, real estate and urban development
Article
20 minutes of reading