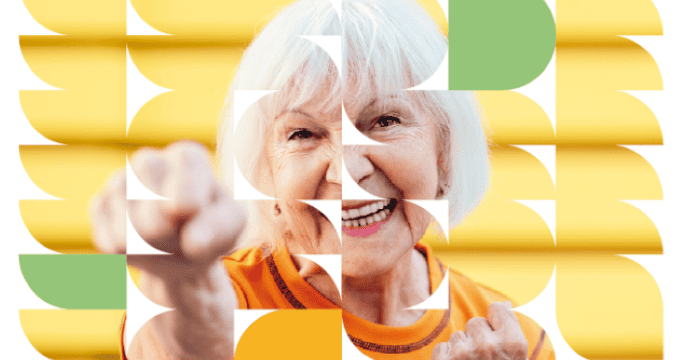
Have robotics already become a reality at all sites?
7 minutes of reading
While there’s no longer any question that robots are an asset for construction sites, increasing their uses involves overcoming a number of hurdles: access to the machines by workers (journeymen), improvement of human / machine interaction, autonomy of robots, financial viability, and so on. There is a complex web of challenges that the construction sector has yet to solve before robotics can become a true ally for construction sites and journeymen. Explanations.
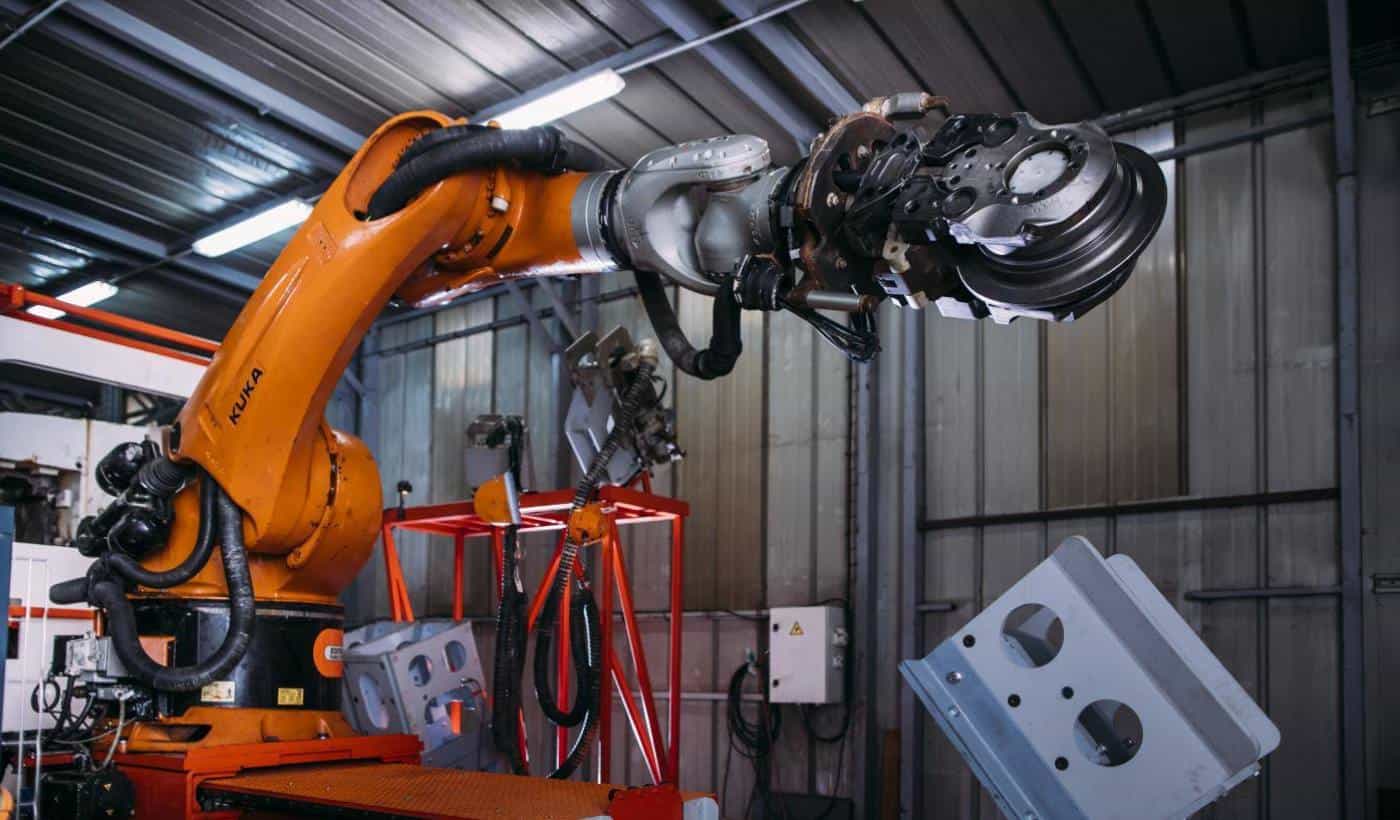
You can be forgiven for thinking that in this ultra-digital era, robotics would automatically appear everywhere, including in the construction industry. However, “robotics and construction are two separate worlds that are not used to communicating with each other,” says Laure Ducoulombier, head of Bouygues Construction’s R&D Design Lab. Two disciplines that are still relatively alien to one another, each with its own separate habits, constraints and languages. That’s why, despite the fact they’re now finally starting to get acquainted, there’s still a long way to go before robots appear at all sites. ”
Public works site: currently the ripest ground for robotics and automation
In 2020, various types of robots were developed and used at Bouygues Construction’s sites in France and abroad. “Large Public Works (TP) sites tend to make greater use of robots, since the contracts are greater in terms of volume, load and budget,” says Philippe Richard, R&D director of the division in charge of ergonomics, productivity and site equipment. “There are a range of different uses. The idea is not only to increase productivity and efficiency at construction sites, but also to reduce the arduousness of some actions that have low added value when carried out by humans. Actions that are often dangerous or that could even end up causing Musculoskeletal Disorders (MSDs). ”

Robots on the front line in Tunnel Boring Machines
While they constitute a workplace for many employees, tunnel boring machines (TMBs) are becoming increasingly automated. A good example of this is the process of changing the cutterheads at the front of these giant cylinders. “Cutters are tools that are used to cut through the terrain and they weigh around 200 kg. For human workers, the task of changing them is a very arduous one. That’s because the area between the front of the TMB and the ground to be excavated is not only cramped but also under pressure, to prevent the ground from collapsing”, says Christophe Portenseigne, Technical Director and R&D Director at Bouygues Travaux Publics. And that’s not the only role robots play in TMBs! Along with Bouygues Construction, they also carry out prevention and analysis tasks. One example is the “Snake” robot (or TMB Inspection Arm) developed in 2012 for a tunnel in Miami. “Small in size, the Snake slides easily into the front of the tunnel boring machine to inspect the condition of all the cutters. Operators can thus easily access precise information about which cutters need to be changed and schedule the necessary maintenance interventions accordingly. ”
Did you know? A fully autonomous robot is being piloted in some TMBs
When a TMB moves forward, prefabricated concrete rings must be installed to support the ground and structure the tunnel’s final lining. Due to their size and weight, the rings are divided into several pieces – precast segments, each of which is still very heavy – that must be fitted into place with extreme precision. Previously, Bouygues Construction teams would steer them using short-range piloting tools controlled via joysticks, for example. In order to reduce the number of people in this dangerous zone and increase the efficiency of the ring positioning process, Bouygues Construction has developed an autonomous robot. In other words: a robot that can find each precast segment of a ring brought in by underground train and place it in the correct position, all by itself.
Automation: a safe and efficient solution for crane operators
Bouygues Construction is also currently in the process of developing assistants specifically designed for crane operators. Purpose: to facilitate the operation of a crane and increase crane operators’ field of vision, alert operators about the presence of a worker near the load carried by the crane, or even automate certain crane activities. A system (Automatic Rotation Control) has already been patented. This system is designed to allow a crane that is not in action (set on vane function) to automatically move outside the work areas of other cranes still in motion. “Such automation will free up the crane operators. They are currently obliged to remain inside their crane when it is not in action, to make sure it stays outside the working area of another crane. ”

Building sites: Robots are being deployed in a limited manner
When it comes to building sites, robot action becomes a more complicated matter. This is due to the cost of the machines and the space they require. “To be financially viable, a robot must be versatile enough to be used at a range of different sites. In addition, building sites have a limited amount of space – and robots require a lot of space. This means that a truly effective system of cohabitation between robots and humans has to be set up. ” To address this requirement, a new generation of robots has been developed, dubbed “cobots”: collaborative robots capable of working in a space shared with humans, and of directly interacting with them. “Cobots are safer for workers. Some, for example, are programmed to slow their movements as soon as they come close to a person. This avoids the constraint of having to enclose those with sharp ends in protective cages. ”

Vignette : A word from the specialist
What’s the future of robotics in the building industry?
“In view of the diversity of tasks and situations at construction sites, intelligence and decision-making should remain the responsibility of the journeymen. Repetitive or strenuous tasks, meanwhile, will be performed by robots. However, for a robot or cobot to be usable on a construction site, the human-machine interface must be easily intelligible to all. This, in itself, poses a real challenge. We must keep developing machines that help digitise and industrialise construction sites while at the same time figuring out how to efficiently tune them into human activity. First of all, it’s clear that interfaces must be as intuitive as a smartphone. They must be as universal and versatile as possible, so that they are easy to use and there’s no need for workers to acquire new authorisations for use. A reliable technical and economic solution must also be found. As an example, we are currently using 3D printers to print building components, but this costs two to four times more than a conventional construction process, points out Laure Ducoulombier, head of Bouygues Construction’s R&D Design Lab division. However, this warrants some reflection, because the 3D printing technique does offer a very real technical advantage: a 3D printer allows us to create concrete components with extremely complicated shapes, which cannot be produced in the traditional way. “
Another criterion for ongoing improvement: “Robots are still struggling to find their way around in buildings under construction,” explains Philippe Richard. Although the robots have comprehensive maps built into them, construction sites are, by definition, constantly evolving in terms of surface area, height, and so on. Likewise, there is always some difference between plans and reality, which can hinder the work of robots. While they definitely have real added value, robots cannot yet match the journeymen’s capacity for adaptation and logical reasoning on a construction site. The challenge, therefore, is to improve the autonomy of robots. ”
More reading
Read also
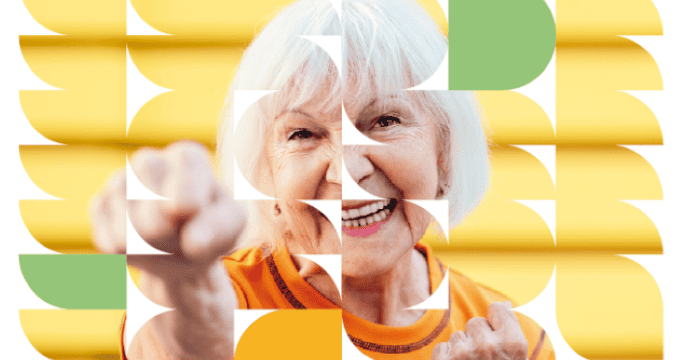
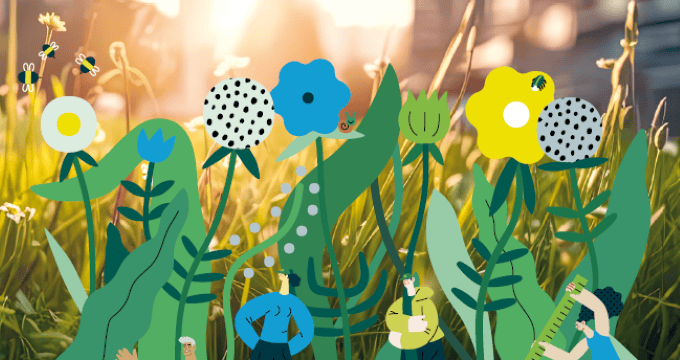
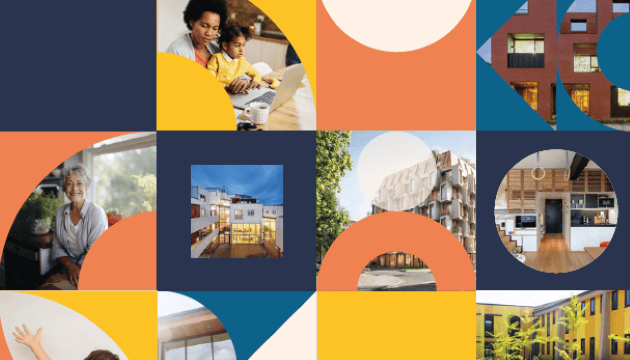
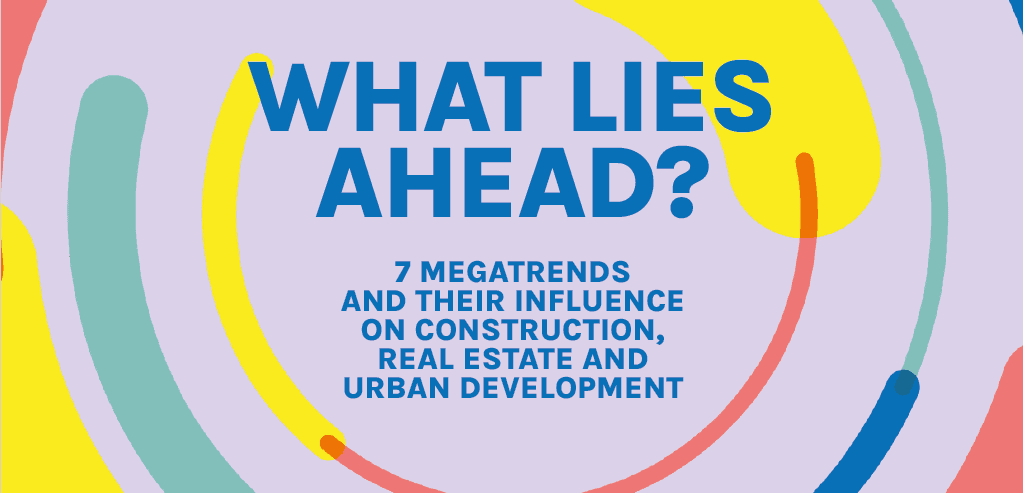
What lies ahead? 7 megatrends and their influence on construction, real estate and urban development
Article
20 minutes of reading