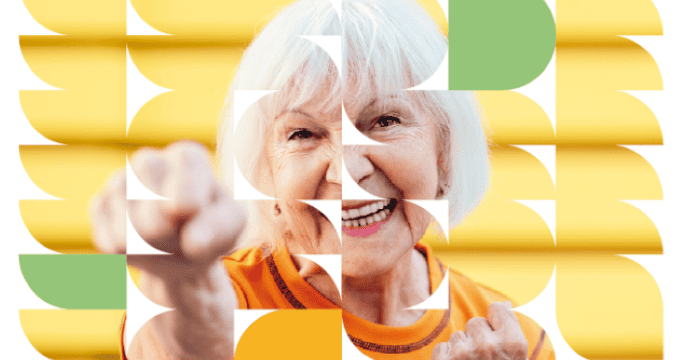
Buildings of tomorrow as materials banks
4 minutes of reading
In mediaeval and Renaissance Rome, the people did not hesitate to use ancient buildings as a source of iron, bricks and other construction materials, just as Spanish settlers did in Aztec and Inca cities, stripping stones from ancient temples to build their own cathedrals. Tomorrow, will we be able to recover reusable components and materials from a building, to be reinvested in a new building instead of throwing them away or recycling them at great cost? This is the idea of the building as a materials bank.
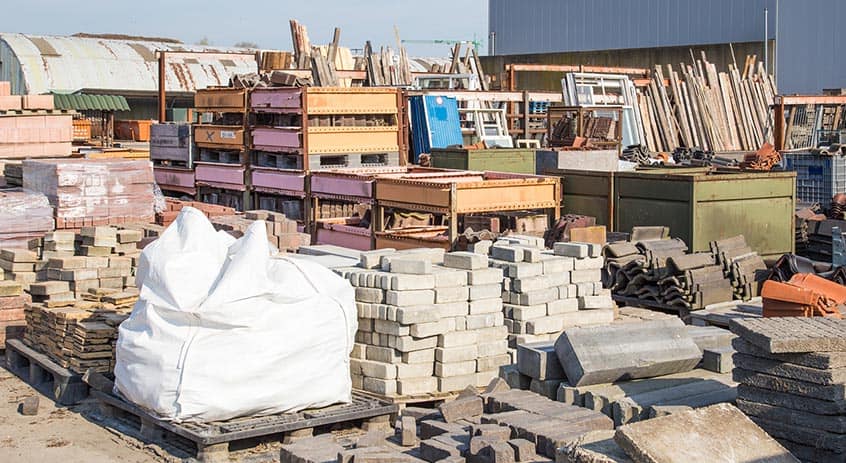
Circular construction
Everyone would agree that to meet environmental challenges, we need to move towards a circular economy that consumes fewer natural resources. Steven Beckers, Michael Braungart and William McDonough have written about the cradle-to-cradle (or C2C) economy. Applied to the urban development, property and construction sectors, this approach can be applied to all stages of a project: programming, design, construction, operation, transformation, etc. In general, three main levers are used: reducing flows by using fewer resources; extending the life of products so as to need to produce less; and closing resource flows, i.e. making better use of products at the end of their lives, their components or their materials. This last lever can be achieved through the use of buildings as a materials bank. When a building is dismantled, a certain amount of waste remains. Some of this waste can be recovered through a transformation cycle; very little of it can be reused on other sites, although inspiring initiatives such as the “Booster du Réemploi” (Reemployment Booster) aim to encourage their recovery. For example, the digital platform Looping brings together materials suppliers from the deconstruction industry with those seeking recycled materials for construction projects. So how can we better anticipate the availability of components?At the core was the data
There is a recurring problem with the recovery of components and materials from existing buildings: we do not know exactly what is in a building. There is no register, no comprehensive list; most existing buildings have at best more or less detailed plans, but very rarely do they have centralised information on the composition of their insulation, the formulation of their concrete or the exact location of their electrical networks. In order to turn the building into a materials bank, we will now need to know exactly what is in the building, how much of it is in the building, what the composition of each material is, and what methods were used to construct it. So why not rely on BIM? Although progress is being made in the design, construction and even gradually in the operation of buildings, BIM digital models are still not widely used for deconstruction. The United Kingdom refers to this as DRIM (“Deconstruction & Recovery Information Modelling”). For newly constructed buildings modelled in BIM, the aim is to maintain and then update a BIM model in line with the evolution of the building over time, specifically through renovations, alterations and wear. This issue is even more complex for existing buildings that do not have BIM: how can inaccessible structural objects be digitised? How can their resistance to wear and tear be tested and evaluated over time? How can unforeseen or hidden damage be taken into account? Is there a need to equip each brick with sensors or, on the contrary, to calculate averages, take safety margins and visually check each element during its deconstruction? What safety margins should be taken? A number of new players are trying to provide answers by using different tools: 3D scanners, high-definition satellite views analysis, maps showing the date of construction and the techniques used at the time, automated analysis using artificial intelligence tools, etc.The BAMB tackles the subject in Europe
Once this work has been carried out, the objects reused in several successive reconstructions will be classified as accurately as possible according to their use and state of wear. In Europe, the BAMB (Buildings As Materials Banks) project is intended to provide “passports” for these materials. The project, funded by the European Union, sets out to initiate circular transformation in the construction sector and is developing prototype software to generate material reuse data sets from digital building models. The platform also aims to go right back to the design stage to advise project managers on the carbon and resource balance of their project and then compare different project scenarios. The purpose is to increase the final re-use rate of each material and component and reduce the negative externalities of construction.More reading
Read also
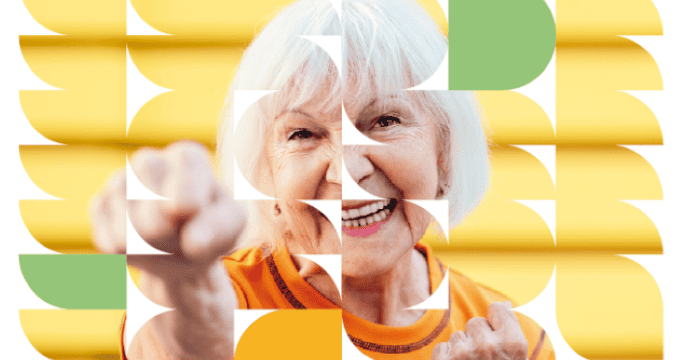
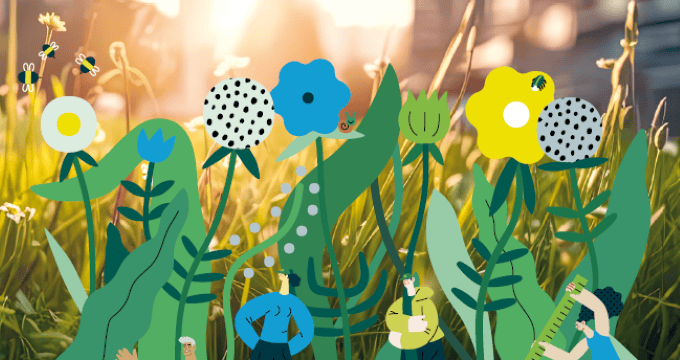
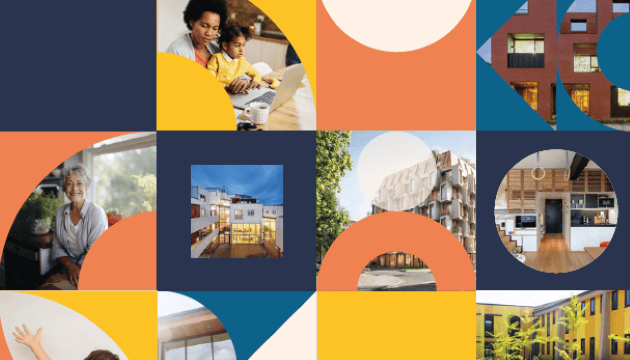
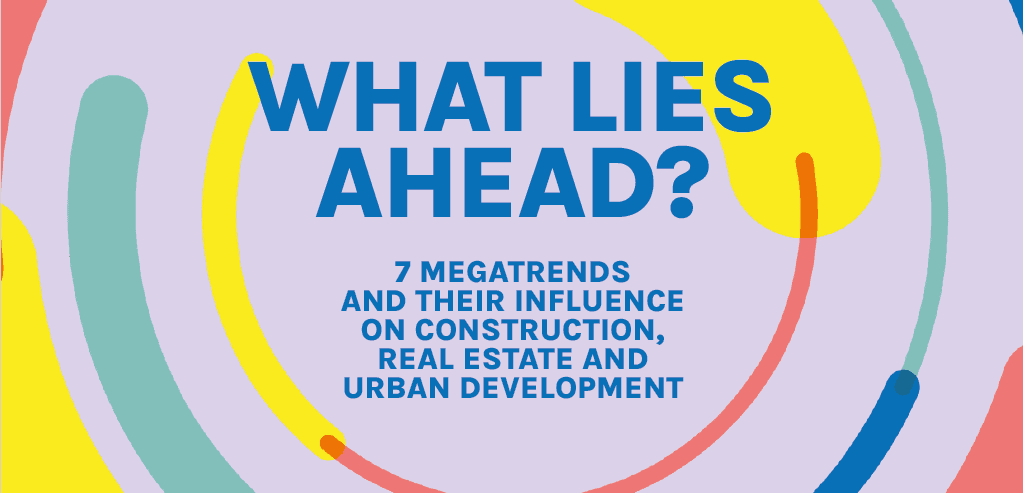
What lies ahead? 7 megatrends and their influence on construction, real estate and urban development
Article
20 minutes of reading