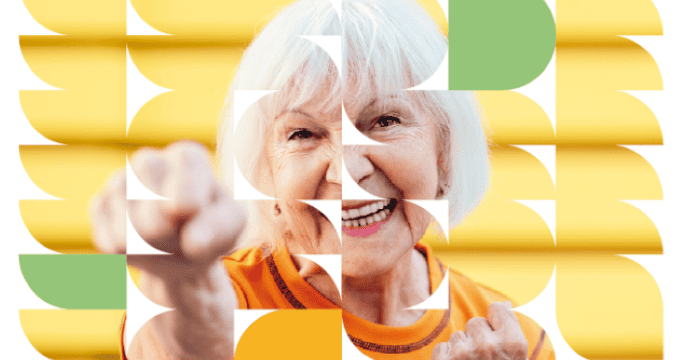
Greener construction, how to build greener?
3 minutes of reading
Across the world, nearly 200 m3 of concrete is poured every second. It is one of the most widely used industrial products – even more so than oil, especially in construction. In spite of its advantages in terms of land development, it is one of the major sources of CO2 emissions due to its cement content. How to build greener?
About one billion tonnes of CO2 is released each year in the world by the cement industry. In the face of such global challenges and future changes in urbanisation, a revolution in construction methods is beginning. How can the construction sector commit to becoming more carbon-free? Can green building meet this challenge?
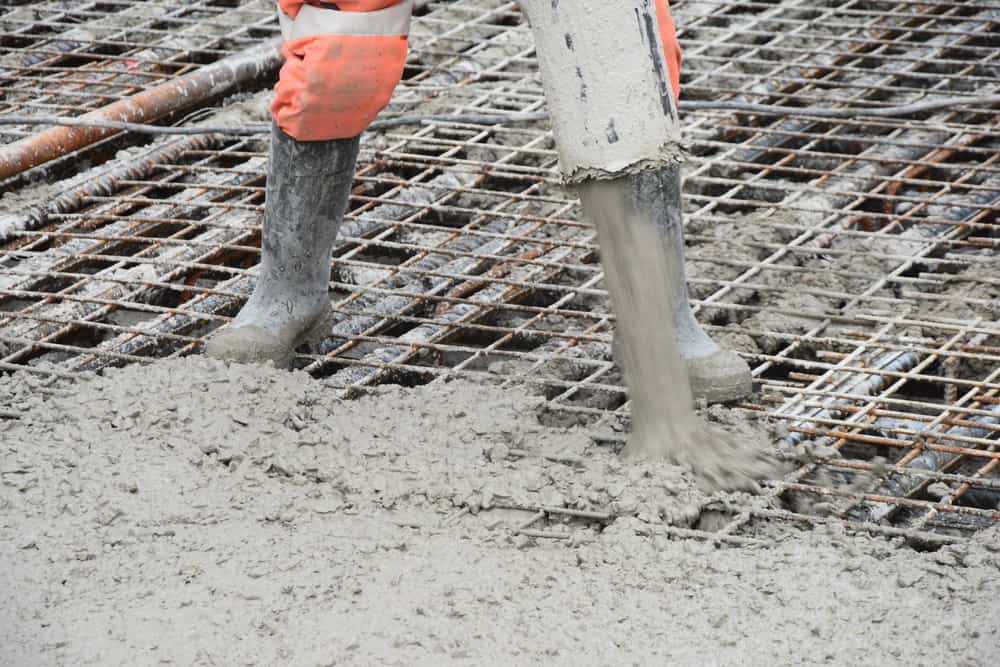
Carbon-free concrete: this is not an oxymoron
Concrete is all around us. It’s present in 90% of buildings and infrastructures. While this universal resource is not to be ignored, new low-carbon building materials are also available. These include construction materials which release low CO2 or no CO2 at all. We obviously know about wood and biosourced materials, such as hemp or linen concrete, but in order to better understand what is meant by ‘carbon neutral concrete’, we must first understand how traditional concrete is made and how this impacts on the environment.Concrete: a material with a high cement content, responsible for 5% of global CO2 emissions
Concrete is largely made from cement, with the addition of aggregates, water and admixtures. The cement alone is responsible for 5% of the world’s CO2 emissions. This significant percentage can be explained in two ways.- Cement is manufactured from a mix of finely crushed rock (limestone, clay and sand) which is heated up in a kiln for 18 hours at 1450°C. CO2 is released as a result of the amount of energy it requires to bake this mixture.
- The release of CO2 from the baked rock. ‘Rocks behave just like trees in that they absorb CO2. Once they are burned, all that CO2 is released,’ explains David Guglielmetti, Development Director at Hoffmann Green Cement Technologies
Innovation: a concrete that divides the carbon footprint by 5
As a result, the carbon issue is therefore pushing key players in the construction industry to reflect on how to reduce greenhouse gas emissions when manufacturing concrete. Hoffmann Green Cement Technologies is a case in point. They have recently signed an agreement with Bouygues Construction concerning the use of an innovative technology called H-EVA (hypertext link to the Hoffman website). This is based on a method which uses no kilns and which therefore releases no carbon. There are also no CO2 emissions from fuel. It allows to divide the carbon footprint by 5 compared to traditional cement. David Guglielmetti believes in disruptive innovation in environmental matters and in the driving force it creates to greatly reduce the carbon footprint. ‘The imperative needed to move towards a low-carbon society in order to meet the commitments made under the Paris Agreement requires a real paradigm shift which can only be brought about by disruptive technologies .’ The economic model is changing, instilling an increased awareness amongst construction companies for the need to create buildings for the comfort of all, buildings which are more sustainable or better recycled using a circular economy approach.Aiming for zero waste on the construction site: construction must give waste a second life
The construction industry must set an example as regards the recycling of waste and the recovery of materials. 79% of non-hazardous waste is recovered by the construction industry in France, which is 9% higher than specified in the Environmental Code* The concept of the circular economy requires a profound change in the way companies and economic players behave. While some regulatory, organisational, technical and even economic resistance has been seen, initiatives are emerging. Some startups are designing digital platforms to serve the circular economy. One example is Hesus. A partner to construction companies, including Bouygues Construction, Hesus puts in place solutions which make it possible to remove, manage and recover materials and waste on construction sites. This startup has developed the Hesus store platform in particular, which allows construction sites to exchange soil. Another example is Ecodrop which offers a waste collection service at construction sites. Local authorities and corporate groups, for their part, are testing prototypes which create channels for the reuse and recycling of materials. Just a stone’s throw from the RER station in Bagneux, Bouygues Immobilier is experimenting with the advantages and disadvantages of selective demolition on a former industrial site. This large urban demolition and renovation project hopes to transform the site into a range of offices and residential units, and aims to recycle 80% of the construction site’s materials. Eurovia and Vinci Autoroutes have completed the first one kilometre section of a ‘100% recycled motorway’ using the same approach. In order to meet the targets for reducing the impact of the 228 million tonnes of waste produced by construction companies in 2019, key players in the sector must continue their commitment for a more sustainable future.* Article L 541-1, paragraph 6
See also: Laure Abdul, PhD in Materials Engineering, presents the concept of soil cement See also: From underground to organic market gardening: recycling excavated soilMost read
More reading
Read also
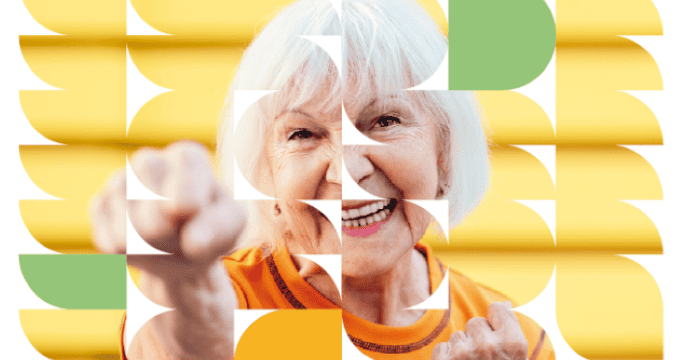
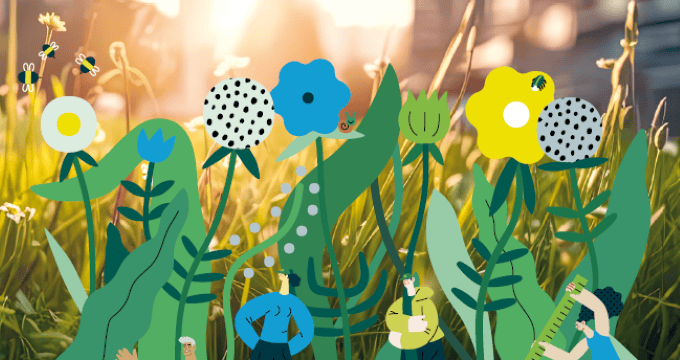
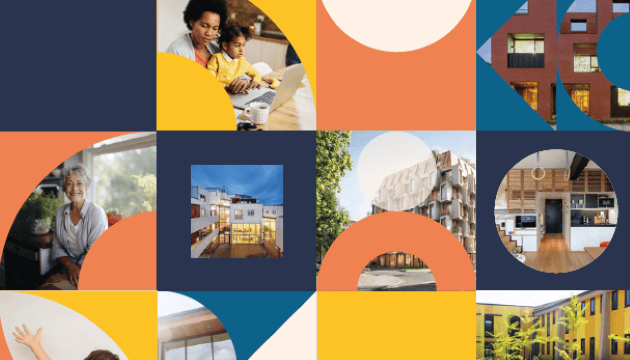
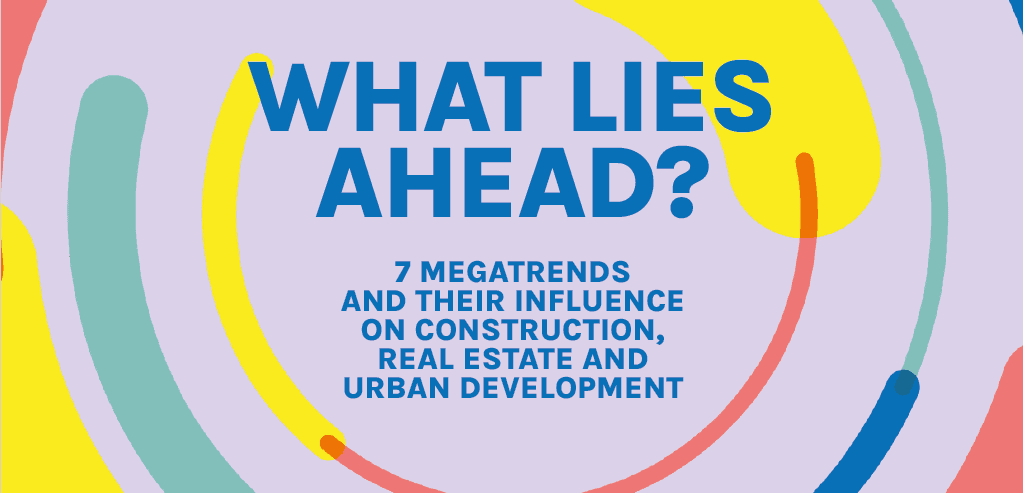
What lies ahead? 7 megatrends and their influence on construction, real estate and urban development
Article
20 minutes of reading